MOULD MANUFACTURING
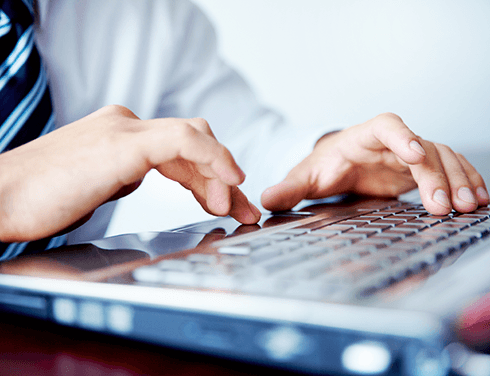
The technical department uses a 3D CAD system to design the moulds.
The large number of cavities, even for complex parts that require special lateral movements and maximum weight reduction of the inevitable sprues, is a characteristic of Bianchi & Giavotti SpA.
Using the mould, designed and made in our own moulding departments, consistently provides all of the information required for ongoing improvement, ensuring the customer both quality and value for the part. Moreover, it ensures a constant mould over time, which is in line with the technical requirements and assumed cycles, and free from excessive and costly maintenance.
TRADITIONAL MOULDING
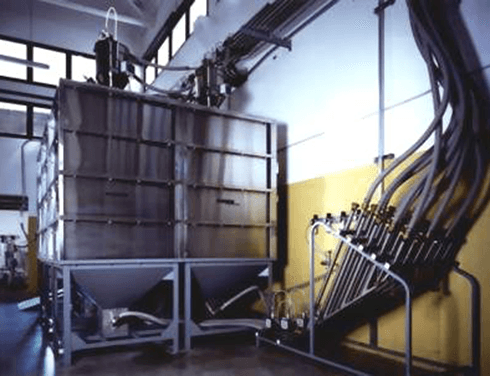
The production departments use 11 injection moulding machines from 100 to 300 tons, organised into 3 shifts over 5 days a week, as well as the Grey Area, where there are 13 presses from 110 to 210 tons that work 7 days a week.
Eight of these presses are in a specific department that ensures that the pieces produced are not contaminated by dust or external agents.
The most frequently used materials are:
- Homo Polypropylene and Copolymer
- HD and LD Polyethylene
- POM
- Polysulfone
- Polyester
- Polycarbonate
- Polystyrene
To visit the production lines and all the various sectors go there now.
CLEANROOM MOULDING / BG PHARMA
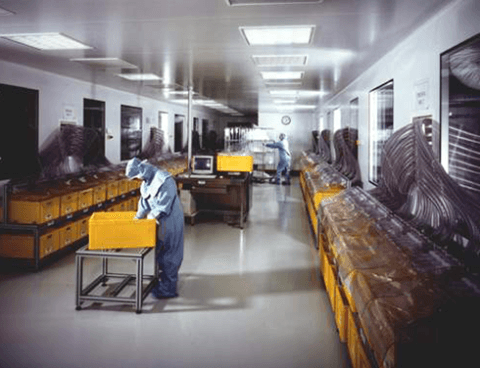
The new facility, located in Via Piemonte 34, San Martino Siccomario, covering around 1000 sqm, sets out to exceed the production limitations of the operating presses of the old facility.
The materials are stowed in dedicated silos and from there, they are transported to the various presses through a system controlled by a PLC using a vacuum line.
The 10 presses in the production department, arranged around the Cleanroom, are all equipped with a robot to remove the parts from the mould and then transfer them to the controlled environment.
Both the mould compartment of the presses and the robot area are protected by an absolute filter (laminar flow) that keeps the part uncontaminated up until it is packaged inside the cleanroom.
The Cleanroom, certified in accordance with class B of the GMP and ISO 7 (formerly Class 10000 of FS 209-E) is equipped with the appropriate areas for staff entry and product output.
A dedicated IT system guarantees perfect traceability of the production, from the batch of the raw material used, the press and the operator, right through to final packaging for the customer.
The Quality system in BG Pharma is certified according to UNI EN ISO 9001:2000 and 13485:2004 and, as well as the product and production process, it also keeps the facility under control, thereby ensuring its efficiency over time.
GREY ROOM MOULDING
From 2010 to today, three new production departments have been implemented named Grey Room 1/2/3.
Bianchi & Giavotti SpA has been engaged in this restructuring through to its completion in 2014.
.
13 presses
have been introduced, including 9 which are fully electric from 110 to 210 tons
that work 7 days a week
(Wittman Battenfeld e Bmb.SpA).
This new air-conditioned department is equipped with anthropomorphic robots that control the handling of the finished products, ensuring speed, better cleaning and overall quality.
Access to this department is managed by dressing procedures and staff action to provide a further guarantee of product quality.
The automated power system for the presses, which is centralised and outside of the department, is a further guarantee of order and cleanliness.
The features described above make the Grey Room production suitable for CHC/OTC category pharmaceutical products and all purposes where absolute quality and cleanliness are paramount.